In the gloomy depths of December 2015, while most aerospace executives were sipping eggnog and celebrating another year of government contracts, SpaceX accomplished the impossible. A Falcon 9 booster touched down with remarkable precision – a feat industry veterans had dismissed as technically unfeasible. Eight years later, established competitors still haven’t replicated what has become routine for SpaceX. The contrast resembles watching traditional automakers struggle with electric vehicles while Tesla races ahead with next-generation technology.
The reusability revolution wasn’t just a visionary concept but a practical solution born from necessity. Engineers who couldn’t afford to waste billions on single-use rockets realized that discarding an entire vehicle after each flight defied economic logic. The resulting 60-70% cost reduction didn’t merely improve accessibility; it fundamentally transformed aerospace economics. What was once considered impossible has become the new industry standard, forcing every competitor to reconsider their approach to spaceflight.
Disclaimer: Some images used for commentary and educational purposes under fair use. All rights remain with their respective owners.
Falcon 9 Rocket Booster
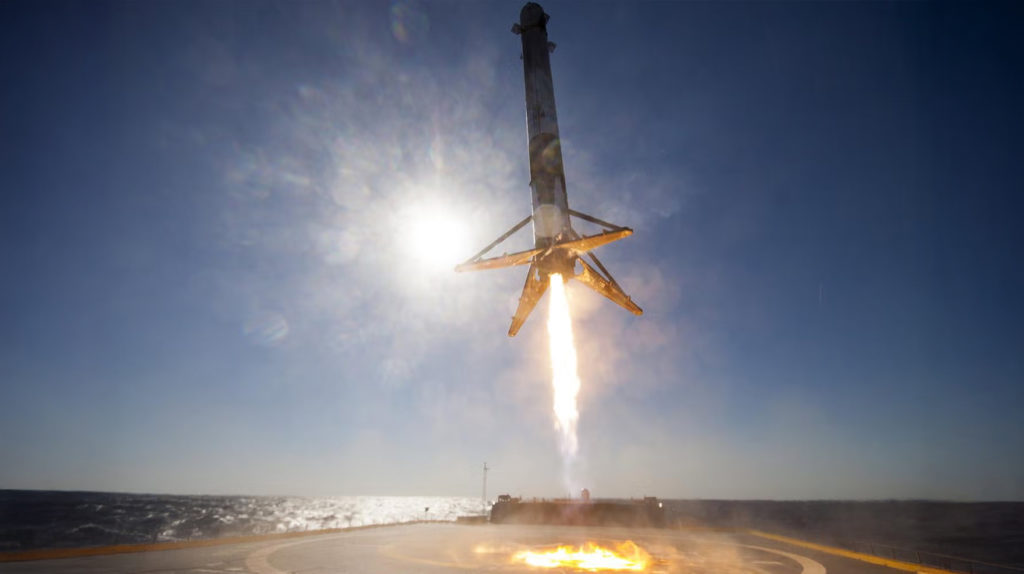
The Falcon 9 booster represents a radical departure from conventional rocket design. While established aerospace companies continued developing expendable launch systems, SpaceX engineered a vehicle capable of returning for multiple missions. This remarkable machine reaches 8,000 kilometers per hour – roughly eight times the speed of sound – then reverses course and lands with astonishing precision. The rocket briefly crosses the Karman Line for about a minute, technically visiting space before beginning its return journey.
Perhaps the most innovative design element sees the engines serving dual purposes as both propulsion and heat shield during reentry. This ingenious solution eliminated the need for additional protective systems while reducing overall weight. SpaceX engineers have successfully executed this complex maneuver over 100 times, transforming what was once considered theoretical into operational reality. The consistency of these landings demonstrates how thoroughly SpaceX has mastered a technology that competitors are still struggling to develop.
Space Shuttle
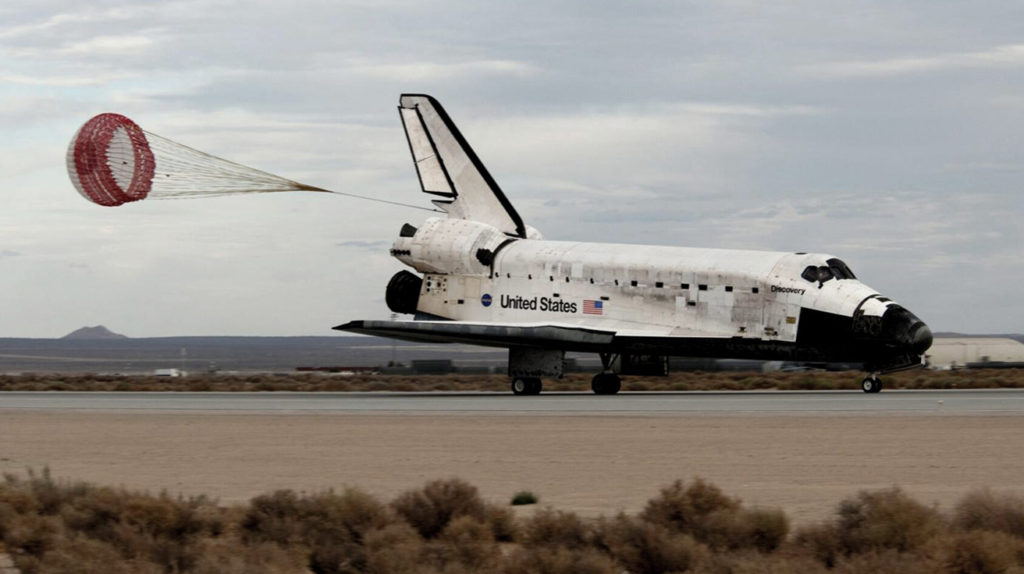
The Space Shuttle program appears remarkably inefficient when compared to current SpaceX capabilities. Each shuttle landing initiated an extensive refurbishment process requiring 650,000 labor hours – equivalent to hundreds of technicians working full-time for an entire year. NASA’s budgetary calculations revealed a startling truth: building entirely new shuttles for each mission would have been more economical than maintaining the supposedly reusable fleet.
Despite these operational challenges, Discovery completed 39 missions across three decades – an average of just over one flight per year. The program maintained a modest pace of five to eight launches annually throughout its 30-year history. By contrast, SpaceX now achieves similar launch frequencies in a single month while operating at a fraction of the cost. This dramatic efficiency differential illustrates how significantly SpaceX has improved upon NASA’s pioneering but ultimately limited approach to spacecraft reusability.
Falcon 9 Version 1
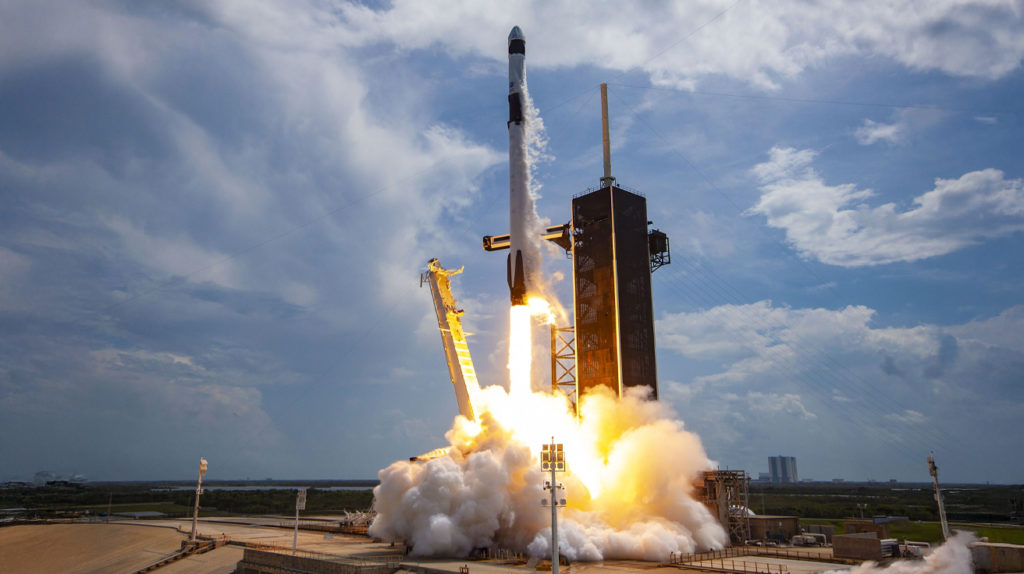
The original Falcon 9 represented the initial phase in SpaceX’s evolutionary approach to reusable rocketry. Standing 46 meters tall and generating 1.1 million pounds of thrust, this early model lacked the sophisticated control surfaces necessary for precise landings. SpaceX hadn’t yet solved the technical challenges of reusability but was methodically building the foundation for future breakthroughs.
Those first five missions established crucial operational experience, including a successful International Space Station cargo delivery that validated SpaceX’s capabilities. While superficially unimpressive compared to later versions, this prototype design provided essential data that informed subsequent iterations. As industry observers questioned SpaceX’s ambitious goals, the company was systematically addressing each technical obstacle that stood between concept and practical implementation of reusable orbital rockets.
Falcon 9 Version 1.1
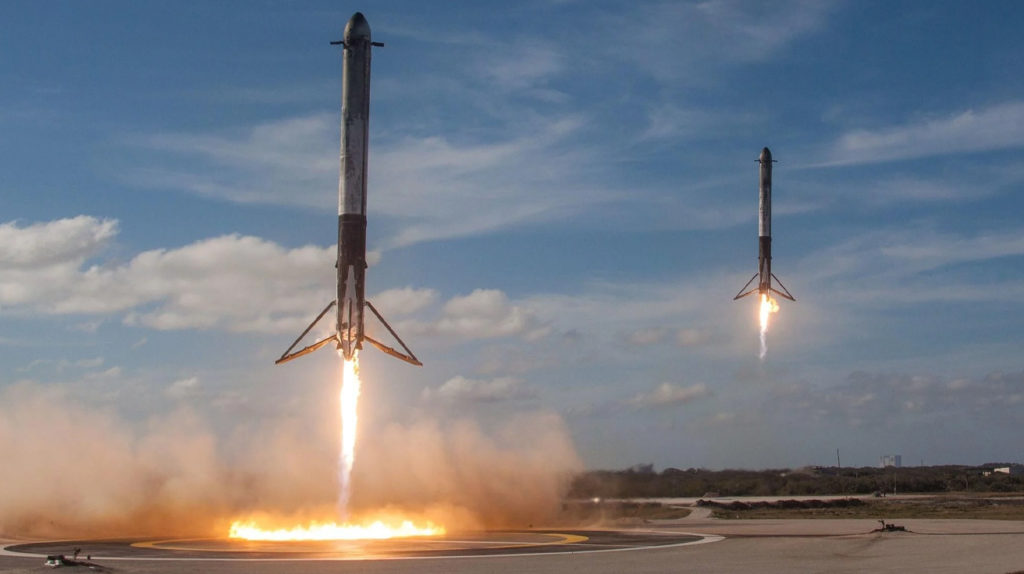
Version 1.1 emerged as a significant advancement, stretching to 68 meters with restructured engines arranged in the more efficient “octaweb” configuration. Thrust increased to 1.3 million pounds, representing substantial performance improvements over its predecessor while maintaining the same foundational architecture.
SpaceX began implementing critical reusability features with CRS-3 introducing landing legs in April 2014, followed by CRS-5 adding essential grid fins for atmospheric steering in January 2015. These components weren’t mere accessories but critical technologies enabling controlled descent. Though no Version 1.1 rockets successfully landed, and one experienced a catastrophic failure in June 2015, these setbacks provided valuable engineering insights. SpaceX’s approach exemplified rapid development methodologies, treating each unsuccessful landing attempt as an opportunity for data collection and design refinement rather than failure.
Falcon 9 Version 1.2 (Full Thrust)
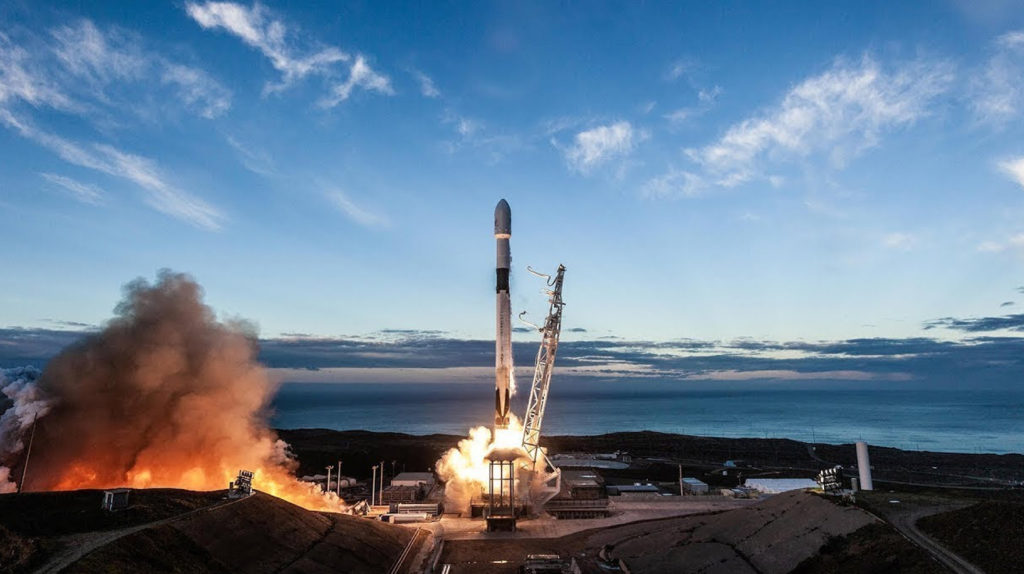
With Full Thrust, SpaceX resolved previous power limitations through comprehensive redesign. Engineers extended the Falcon 9 to 70 meters and increased thrust to 1.7 million pounds – substantial improvements that enhanced payload capacity. The technical team implemented supercooled propellants, effectively increasing density to maximize fuel volume within existing tank dimensions.
This iteration achieved the historic first successful landing at Cape Canaveral, validating years of theoretical work and failed attempts. While Full Thrust underwent continuous refinement, its fundamental architecture remained consistent. NASA eventually certified this version for human spaceflight – official recognition of SpaceX’s safety and reliability standards. Throughout this development period, SpaceX maintained an aggressive iteration schedule that consistently outpaced traditional aerospace timelines by years rather than months.
Falcon 9 Block 5
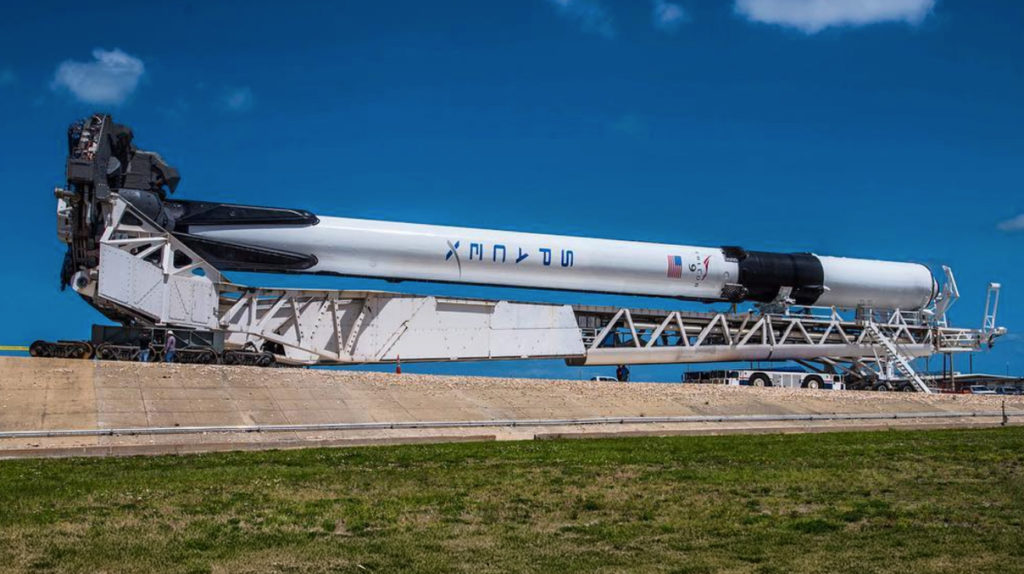
Block 5 stands as the culmination of SpaceX’s iterative design process – the definitive version incorporating lessons from every previous test and operational flight. Maintaining the 70-meter height while increasing thrust to 1.8 million pounds, its distinctive partially blackened appearance results from functional thermal protection rather than aesthetic choices.
Engineers implemented comprehensive upgrades throughout the vehicle: improved Merlin engine turbo pumps, titanium grid fins replacing aluminum for superior heat resistance, and enhanced thermal protection across the entire structure. The redesigned landing legs gained retraction capability, streamlining recovery operations and accelerating turnaround time. Block 5 doesn’t merely represent incremental improvement but the maturation of SpaceX’s reusability concept into a fully operational system with reliability metrics surpassing many expendable alternatives.
Falcon 9 Block 5 Reusability
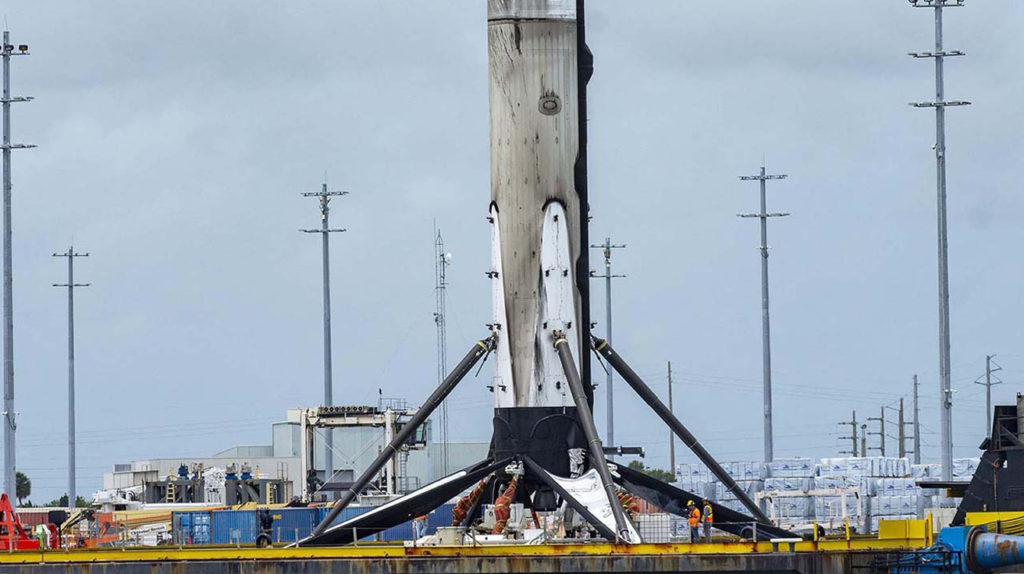
March 2017 marked the operational debut of SpaceX’s reusability program with the first refurbished Falcon 9 launch, transforming theoretical cost savings into commercial reality. By July 2024, booster B1058 – which previously carried astronauts to the ISS in May 2020 – completed its sixteenth successful flight, establishing unprecedented reuse capabilities for orbital-class rockets.
These sixteen missions occurred over just three years – a turnaround efficiency that revolutionized launch economics. Initially certified for ten flights, SpaceX gradually extended Block 5’s operational lifespan to fifteen launches in 2022, and now qualifies B1058 for up to twenty missions. Engineering analysis suggests these boosters could potentially achieve sixty launches with appropriate maintenance protocols, representing a sixfold increase over original specifications. This exceptional durability transforms the economic model of orbital launch services, creating competitive advantages that established providers struggle to match despite decades of industry experience.