The simplicity of golf is its greatest con job. You hit a ball with a club. Straightforward enough until you realize that seemingly innocent little white orb holds more engineering secrets than NASA’s backup servers.
Look beneath the dimpled exterior and you’ll find a world where obsessive perfectionists wage daily battles against physics. Those basic clubs and balls conceal designs that marry old-world craftsmanship with space-age materials—kind of reminds you of that scene in “The Prestige” where the simple magic trick required years of innovation behind the curtain.
Understanding the manufacturing behind your gear won’t just satisfy curiosity. It might actually save you three strokes. Next time you skull a wedge across the green, remember: it’s not the arrow, it’s the archer. Usually.
Disclaimer: Some images used for commentary and educational purposes under fair use. All rights remain with their respective owners.
Wound Golf Balls
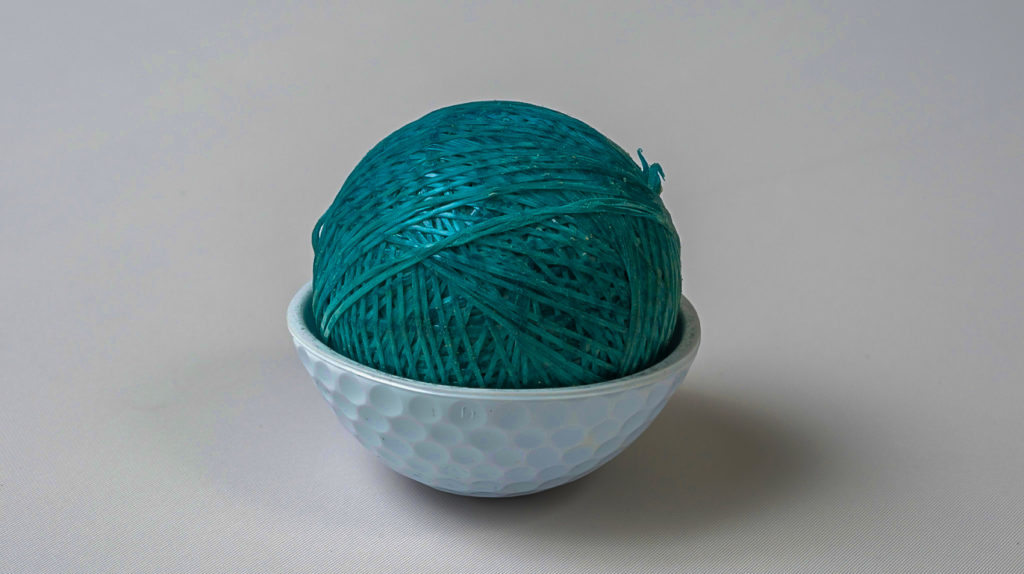
There’s something almost sacred about wound golf balls in an era when everything keeps getting “optimized” to death. They’re golf’s vinyl records in a streaming world—less convenient but somehow more authentic.
Pro shops don’t stock many anymore, but purists still hunt them down like craft beer enthusiasts seeking a limited release IPA. These beauties get crafted through a process that would make a Swiss watchmaker nod: rubber thread wrapped with monk-like patience around a center core. While today’s premium multilayer urethane balls have narrowed the gap, wound balls maintain a devoted following. The construction creates a softness that lets skilled players shape shots like sculptors. For golfers who care more about artistry than bombing it past the 300-yard marker, these wound balls offer a distinct playing experience that modern technology still tries to emulate.
Two-Piece Golf Balls

Let’s face facts—most of us aren’t exactly channeling Tiger circa 2000 out there. We’re more “Tiger King” than Tiger Woods. That’s why the majority of us mere mortals opt for two-piece golf balls.
The construction couldn’t be more straightforward: solid rubber core wrapped in a tough outer shell more dimpled than a teenager with bad acne. Ball makers keep this design basic for a reason—maximum distance while keeping costs low enough that you won’t need therapy after dumping a sleeve into the lake. At around $20 per dozen, losing them hurts about as much as a paper cut.
That harder exterior actually helps your wayward swing by reducing those embarrassing banana slices. It’s the golf equivalent of bowling with bumpers, and weekend warriors everywhere silently thank the engineers while pretending it was pure skill that kept that drive in play.
Golf Ball Core Formation

Next time you crush a drive (or more likely top it 40 yards), consider the Willy Wonka-esque factory where your ball’s heart came to life. The core formation starts in industrial facilities where rubber compounds transform through a process that makes sourdough bread preparation look simple.
The bouncy rubber gets mixed with chemical additives that manufacturers guard more closely than Augusta National guards its membership list. This concoction heats until it becomes a sticky batter before going through precision extruders. Out pop these bizarre marshmallow-shaped slugs bearing zero resemblance to golf equipment. Each manufacturer has their own closely-guarded specifications for temperature and duration during the baking process. These proprietary settings transform soft rubber into something with the exact properties needed to launch off your driver face at ridiculous speeds.
Golf Ball Shell Formation
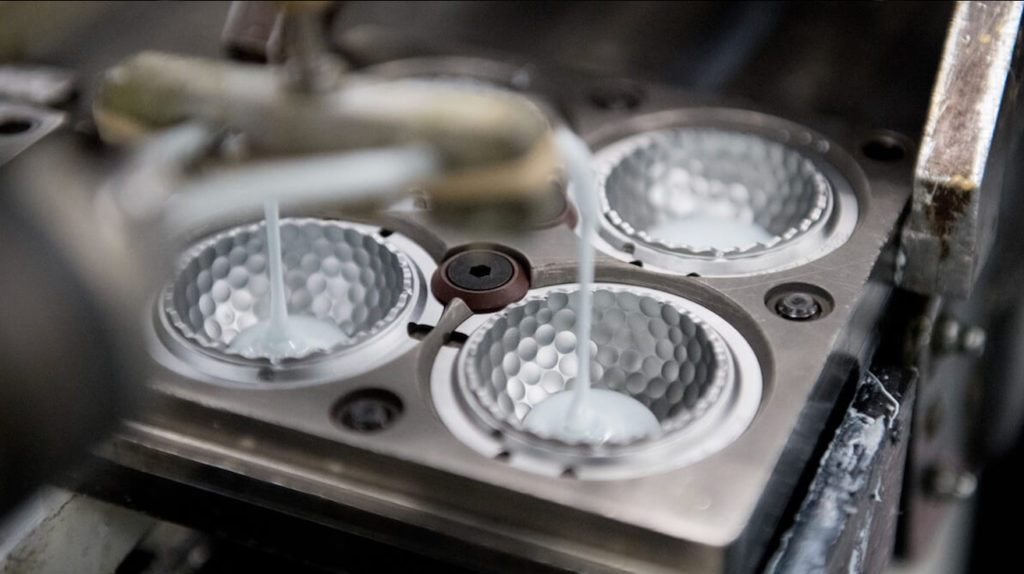
Those dimples aren’t just cute facial features—they’re aerodynamic marvels that make the difference between your ball flying like an eagle or a wounded duck. Creating them requires engineering that would make NASA nod in appreciation.
Manufacturers heat thermoplastic material until it flows like maple syrup, then inject it under pressure into specialized molds. Each cavity contains the negative impression of the ball’s surface, complete with those scientifically calculated dimple patterns. The machines spit out four dozen finished shells every minute—faster than most hackers lose balls in a round at Sawgrass. Once cooled, these shells await their marriage to the cores, transforming into those pristine white spheres destined for greatness—or more likely, the bottom of the pond on the par-3 12th.
Golf Ball Finishing and Quality Control

The final stages of golf ball production might be the most impressive part, or as they say in Caddyshack, “the Cinderella story” where the ugly duckling transforms into a tournament-ready beauty.
After core and shell come together, automated milling machines trim excess plastic with micron-level accuracy. Quality inspectors verify perfect spherical shape at multiple checkpoints. Any ball falling short gets yanked faster than a putt that missed the break. Robotic arms stamp on logos and numbers with sci-fi precision, instantly UV-dried to prevent smudging. A protective polyurethane coating adds that distinctive sheen while improving durability. The freshly coated balls then spend exactly 5 minutes drying at 150°F before packaging. All this technology, precision, and expense just so you can three-putt from 15 feet.
Wooden Golf Club Head Shaping
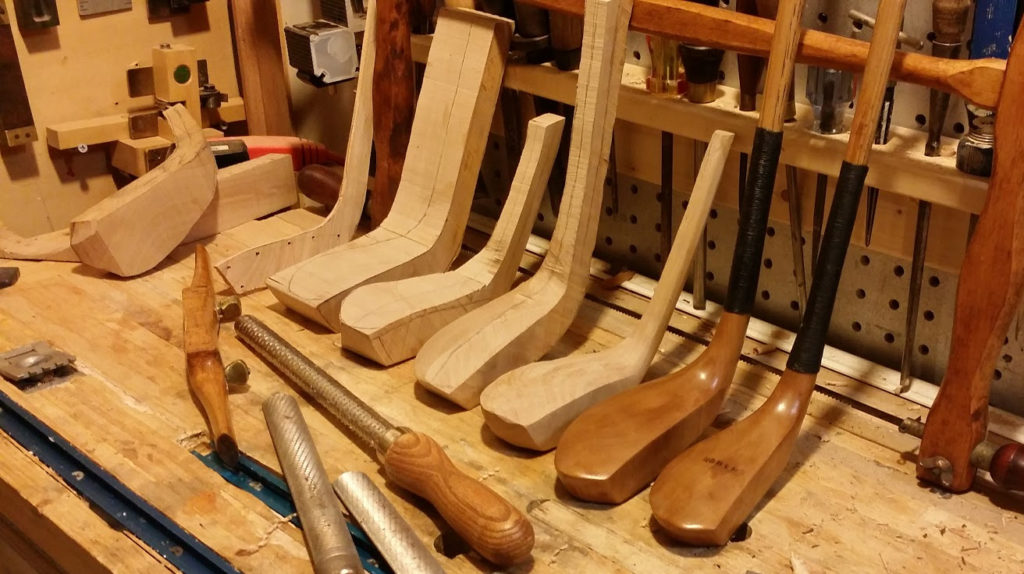
When golf nerds get misty-eyed talking about persimmon, they’re not discussing fruit salad ingredients. The creation of wooden club heads marries Old World craftsmanship with subtle artistry in a way that makes modern manufacturing look soulless.
Everything starts with premium persimmon wood selection—chosen for density and grain patterns. Craftspeople quarter-saw these logs with careful precision to ensure grain runs exactly right for maximum structural integrity. Specialized duplicating machines follow master model contours, carving each piece to exacting specs. A cutting tool carves a precise slot across the future striking face to house reinforcing plastic. Perhaps most impressive is the router work creating that elegant hourglass-shaped cavity beneath for the metal sole plate. The sheer labor intensity explains why collectors treat these clubs with reverence typically reserved for religious artifacts and rare bourbon.
Wooden Golf Club Head Weighting and Finishing
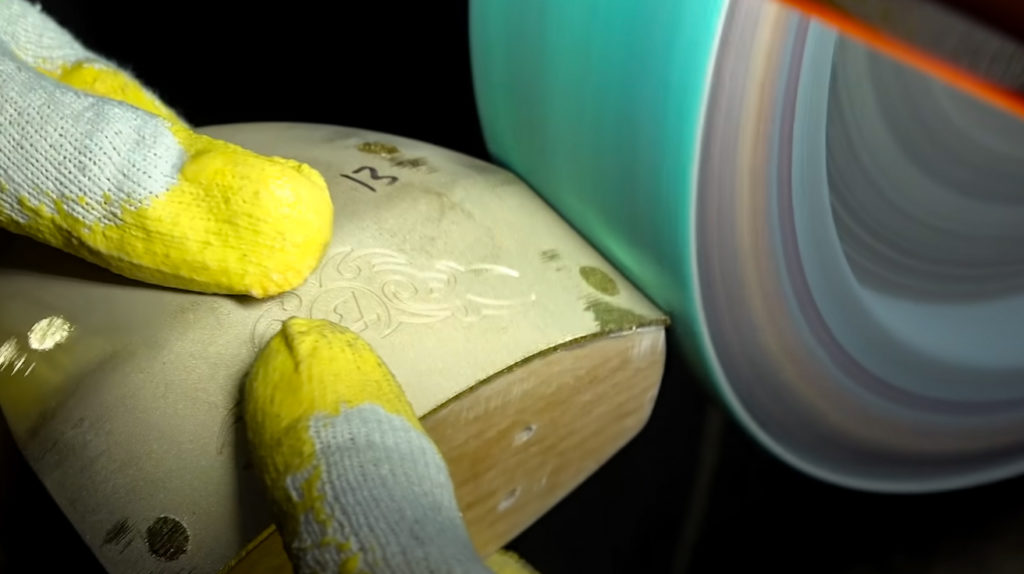
What separates a garden-variety wooden club from the kind Ben Hogan would actually deign to hit? It’s all about weight balance—and manufacturers obsess over it with the intensity of a putting stroke over a 4-footer to win the club championship.
The tolerances would make a NASA engineer nervous. Each club head must fall within 3 measly grams of target weight. Craftspeople achieve this by strategically positioning lead pellets throughout the head. A precisely fitted stainless steel sole plate gets installed on the bottom, protecting the wood while adding just enough additional heft. Look closely at any quality persimmon driver and you’ll notice fine grooves on the face—each line scored by technicians using what amounts to a jeweler’s saw. After shape and weight perfection comes the staining process, followed by five separate layers of protective polyurethane, creating that gorgeous glossy finish worthy of both golf bags and museum displays.
Wooden Golf Club Assembly
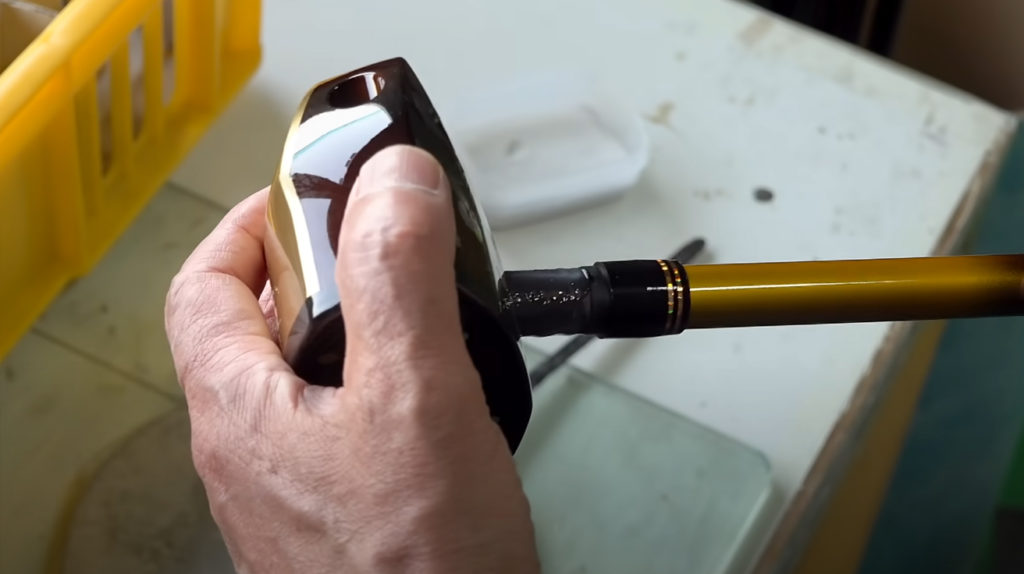
The marriage of shaft to head in wooden clubs involves more precision than a heart surgeon needs on a Monday morning. It’s this assembly process that separates heirlooms from kindling.
First comes securing a metal sleeve inside the neck using specialized adhesives. The sleeve creates that critical connection point for the shaft, which must align with mathematical precision. Getting the shaft alignment even 1 degree off is the equipment equivalent of missing the fairway by 30 yards. Once proper alignment’s achieved, craftspeople add precisely measured amounts of pulverized lead for weight fine-tuning. When complete, a proper wooden club represents harmony between tradition and innovation that delivers both classic beauty and functional excellence.
Motorized Golf Cart Frame and Body Assembly

Golf carts have evolved from glorified wheelbarrows to something closer to luxury automobiles. Today’s models have more engineering DNA from Tesla than from those rickety pull carts your grandfather complained about.
Everything starts with the frame—manufacturers have mostly switched to aluminum I-beams that bring remarkable structural strength without unnecessary weight. Smart material choice improves both efficiency and handling, turning potential cart paths into miniature Autobahns. The seating deserves special mention: marine-grade plywood platforms (selected for weather resistance) covered with vinyl over supportive foam padding. These ergonomic thrones make a huge difference during five-hour rounds when your buddy keeps looking for balls in places Lewis and Clark wouldn’t explore. Power comes from surprisingly sophisticated 48-volt electric motors that run cleaner and quieter than a well-oiled putter stroke. Beyond just moving players around, these eco-friendly powerplants align perfectly with golf’s growing environmental consciousness—because nothing says “appreciation of nature” quite like driving through it rather than walking. Impact-resistant plastic body panels shield the expensive bits from inevitable encounters with tree trunks, coolers, and that one guy who keeps forgetting to set the parking brake. The result? A perfect balance of comfort and durability that makes modern cart rides almost as enjoyable as making a birdie. Almost.
Motorized Golf Cart Powertrain and Component Installation
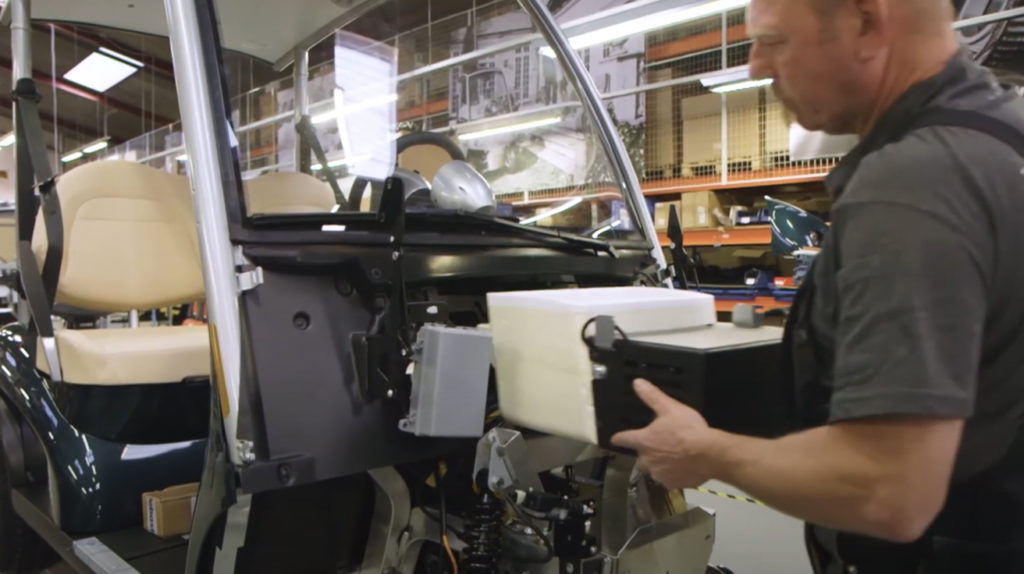
Don’t be fooled by their casual appearance—modern golf carts pack enough engineering complexity under their plastic skins to make a mechanical engineer spill his Arnold Palmer.
The heart of any cart is its electric powertrain, a compact marvel that would impress Elon Musk if he ever took a break from ruining Twitter to play golf. Assembly begins with technicians positioning the axle assembly directly atop the differential—a setup maximizing power delivery while minimizing energy waste. The 48-volt electric motor gets bolted to mounting points using fasteners torqued to exact specifications. This precision matters—any excess vibration would make the cart feel as refined as a $2 putter from a garage sale. Power transfers from motor to wheels through an integrated transaxle, essentially a simplified transmission optimized for the stop-start nature of course navigation. The batteries typically occupy the rear compartment—not just for convenience but to balance weight distribution in a way that prevents the cart from doing wheelies when your buddy stomps the accelerator after three beers. Four thick wires connect these batteries to the motor controller, forming the electrical lifeline of the whole operation. Governing everything is an electronic control module—the cart’s silicon brain—that manages acceleration, speed, and power output with greater care than most of us manage our actual golf swings.
Motorized Golf Cart Quality Control and Finishing
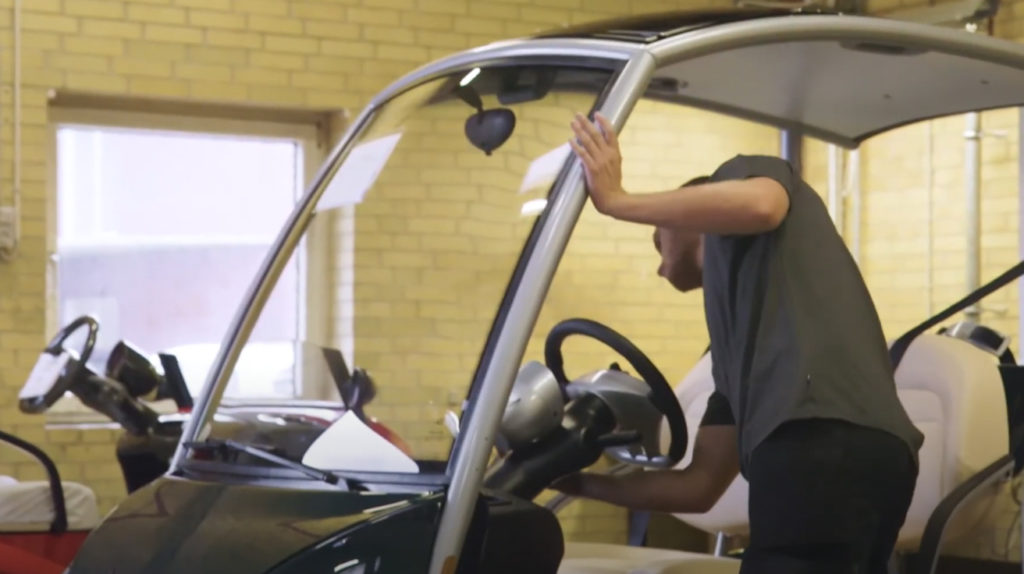
You might think golf cart manufacturing involves about as much quality control as a kid’s lemonade stand. You’d be dead wrong. These facilities run tighter ships than the Secret Service protecting a presidential foursome.
During assembly, sophisticated computer systems monitor torque values at numerous connection points. Each fastener must hit precise specifications—too loose and things rattle apart faster than a weekend hacker’s swing; too tight and components crack under pressure. Safety regulations mandate carts cannot exceed 15 mph—a restriction built into control systems. The seating installation receives special scrutiny: front and rear benches must fit with perfect alignment. Once assembled, specialized lift systems carry each cart through final inspection where technicians verify everything from turn signals to brakes. Only after clearing these hurdles does a cart receive final blessing to transport golfers and their increasingly ridiculous array of accessories around the course.
Stainless Steel Golf Club Head Casting
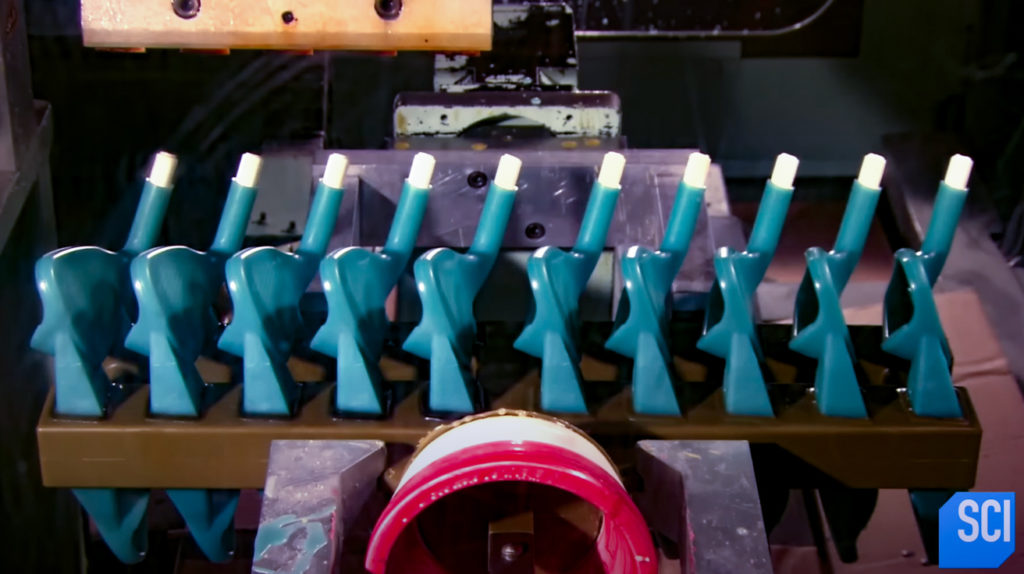
The birth of a modern stainless steel club head involves processes more akin to medieval alchemy than manufacturing. It’s the equipment version of “Game of Thrones”—fire, metal, and occasional shouting.
Everything begins with creating perfect wax duplicates of the club design. Technicians inject heated wax into molds detailed enough to capture fingerprints. These wax models get coated with specialized ceramic material, each layer strengthened with silica sand. Meanwhile, workers heat stainless steel bars to 3000°F while ceramic molds reach 1800°F. When both hit optimal temperatures, workers pour molten metal into the heated molds, causing the wax to vaporize completely (hence “lost wax casting”). After cooling for 5 hours, workers break away the ceramic shells, revealing newly-formed club heads. The process combines industrial precision with dramatic flair that would make for riveting television if the History Channel ever runs out of pawn shop shows. ceramic molds themselves undergo preheating to about 1800°F.
When everything reaches the proper temperature, foundry workers carefully pour the molten steel into the heated ceramic molds. The extreme heat causes the wax inside to vaporize completely (a technique appropriately called “lost wax casting”), leaving a perfect cavity for the metal to fill.
After cooling for approximately 5 hours, the now-solid metal club heads are ready for extraction. Workers carefully break away the ceramic shell using specialized hammers, revealing the newly-formed club heads inside. It’s a dramatic moment – like cracking open a geode to reveal the treasure within.
Stainless Steel Golf Club Finishing and Assembly
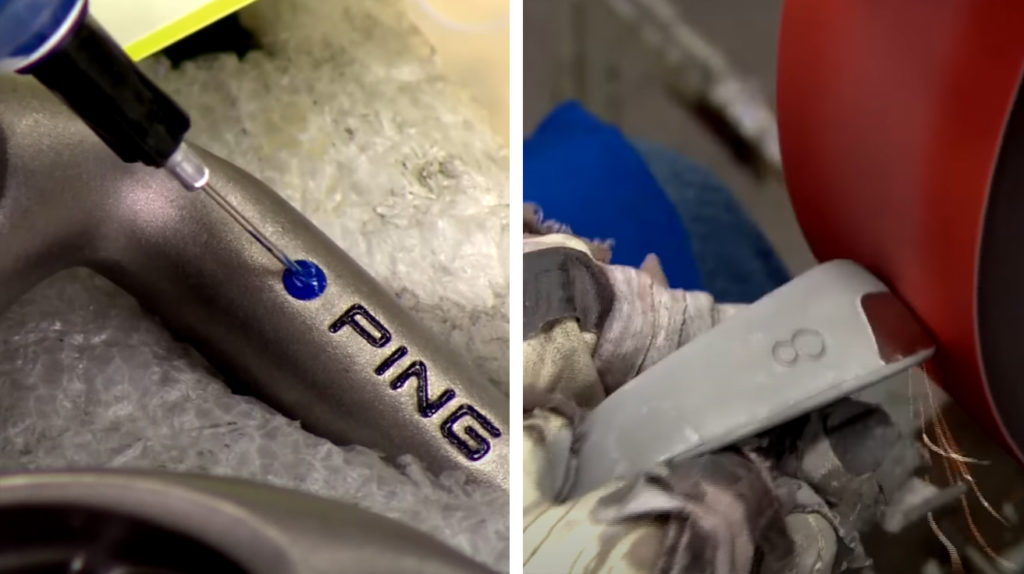
Raw cast club heads resemble prehistoric tools more than precision sporting equipment. The transformation from caveman relic to pro shop beauty requires more steps than Augusta National par-5.
First comes sandblasting to create specific surface textures that affect performance. Different zones need different finishes: the face requires one texture for proper ball contact, while the sole demands another for turf interaction. Next, technicians attach those shiny badges that provide critical model information. Club identification continues with automotive-grade paint marking each precise loft angle. Before the shaft meets head, workers apply specialized epoxy to connection points—engineered specifically to withstand the violent forces created by weekend warriors trying to kill the ball. Assembly culminates with pneumatic hammers driving shafts into position. The result? A club delivering consistent feel and performance—at least until you blame it for your slice into the executive parking lot.
Golf Club Shaft and Grip Installation
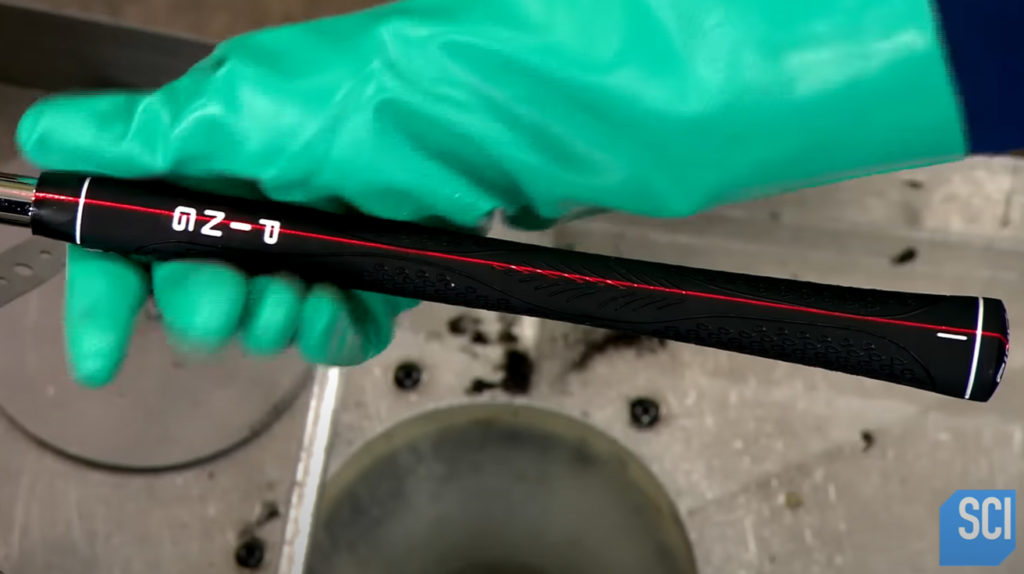
That part of the club you actually touch might seem basic as toast, but grip installation involves engineering sophisticated enough to make Silicon Valley nerds sweat.
Before anything happens, technicians cut each shaft to precise length. The right length depends on player height, arm length, and swing characteristics—even a quarter-inch difference can transform a potential birdie into a disaster. Workers wrap the upper 10 inches with specialized double-sided tape engineered specifically for this purpose. Modern grips feature advanced materials balancing tackiness and durability. Getting them perfectly straight matters tremendously, which is why manufacturers increasingly employ laser alignment systems. Next time you blame equipment for your flubbed chip, remember: someone used actual lasers to ensure your grip was installed with the precision of neurosurgery. the upper 10 inches with specialized double-sided tape engineered specifically for this purpose—with adhesive properties balanced between immediate tack and long-term bonding that would make relationship counselors jealous. Modern grips feature advanced materials balancing tackiness, shock absorption, and durability. Getting them perfectly straight matters tremendously—even tiny misalignment can cause subtle swing problems that accumulate faster than bogeys on a windy day. That’s why manufacturers increasingly employ laser alignment systems guaranteeing perfect positioning. Next time you blame equipment for your flubbed chip, remember: someone used actual lasers to ensure your grip was installed with the precision of neurosurgery, making your excuse weaker than gas station coffee.
Golf Club Angle and Weight Adjustment
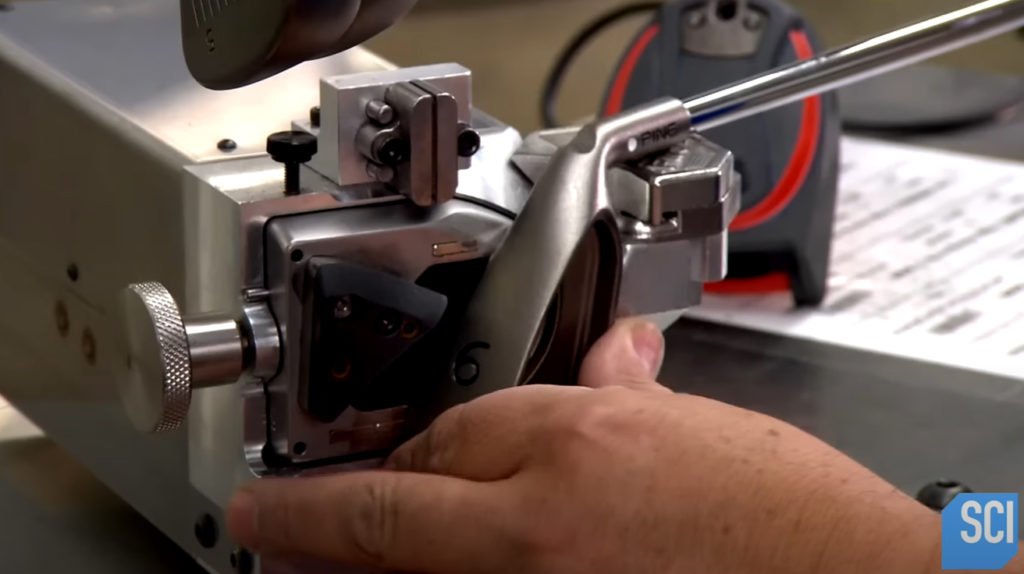
The days when club adjustments happened by eyeball and feel disappeared faster than free range balls at a public driving range. Today’s process resembles a laboratory scene from a sci-fi movie.
Modern club fitting employs computer systems that measure with accuracy that would make Swiss watchmakers slow-clap. Specialized diagnostic equipment detects variations in lie and loft angles down to 0.1 degrees—differences invisible to the naked eye but capable of sending your ball to neighboring zip codes. After measurement comes adjustment, sometimes involving subtle hosel bending. Weight adjustment involves positioning an 18-gram weight (actually closer to 17.7 grams to accommodate epoxy mass) with surgical precision. This fanatical attention to detail explains why professional clubs perform with remarkable consistency. Unfortunately, all this precision still can’t fix your over-the-top move that sends balls screaming toward the parking lot.
This process makes approximately 3,000 finished tees, demonstrating remarkable material efficiency. The logs first progress through an automated debarking process. This machinery removes the outer layer and any surface impurities. A specialized slasher saw then cuts the logs to optimal processing length. These preparatory steps create the raw material foundation for manufacturing consistent, high-quality tees.
Wooden Golf Tee Manufacturing: Log Preparation
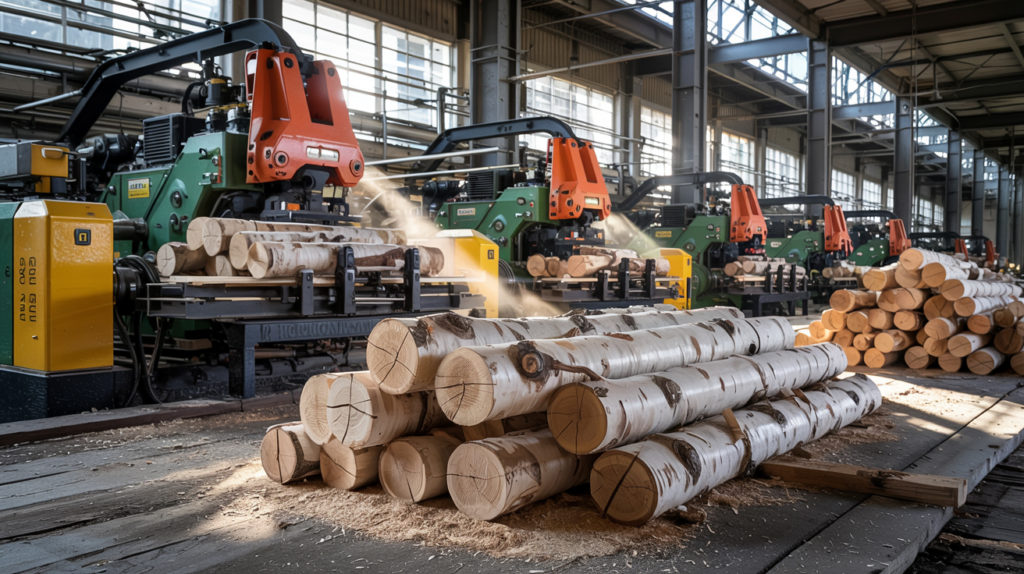
Some say legend began with a simple wooden tee. White birch is scaled for tee production. Just one 8-inch log yields many tees. It makes almost 3,000 tees from one log. The logs go through a debarking process. This removes the outer layer and impurities. A slasher shortens the logs. These steps ready the wood for tees.
Wooden Golf Tee Manufacturing: Dowel Formation
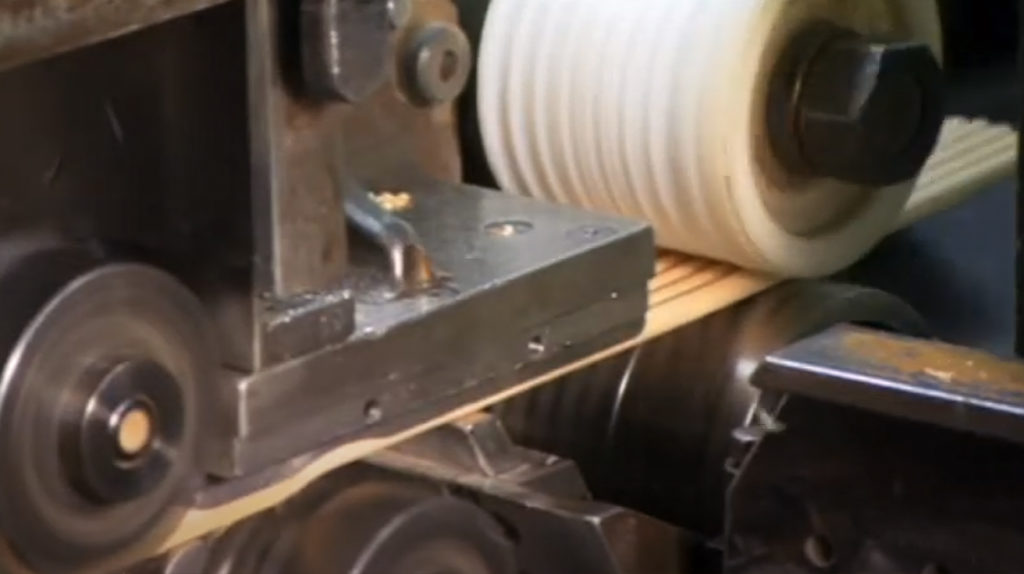
Transforming raw lumber into those perfectly shaped tees involves more industrial might than most golfers imagine while absentmindedly jabbing them into the turf.
Industrial-grade saws slice boards into manageable dimensions with the efficiency of a tournament rules official shutting down creative interpretations of “casual water.” These machines transform 4.5-inch boards into narrower sections measuring approximately 18 inches long. High-speed molding machines grip these rectangular pieces and rapidly spin them against cutting heads, reshaping them from squared lumber into perfectly round dowels smoother than a tour pro’s putting stroke.
Wooden Golf Tee Manufacturing: Quality Control and Shaping

Quality inspectors evaluate dowels with standards stricter than Augusta National’s member selection committee. These eagle-eyed professionals don’t mess around with mediocrity.
Trained personnel sort approximately 19,000 dowels hourly, ensuring only perfect specimens continue the journey. Specialized racks secure these approved dowels, each holding up to 8,900 individual pieces. A precision lathe then shapes each dowel into a rough profile faster than a marshall speeds toward slow players. The final transformation happens through the “trumpet,” a specialized tool that simultaneously sculpts and slices each tee to length. The distinctive cup formation develops naturally during separation, creating the perfect cradle for your ball before you thin it thirty yards directly into the group ahead.
Wooden Golf Tee Manufacturing: Sanding and Sorting
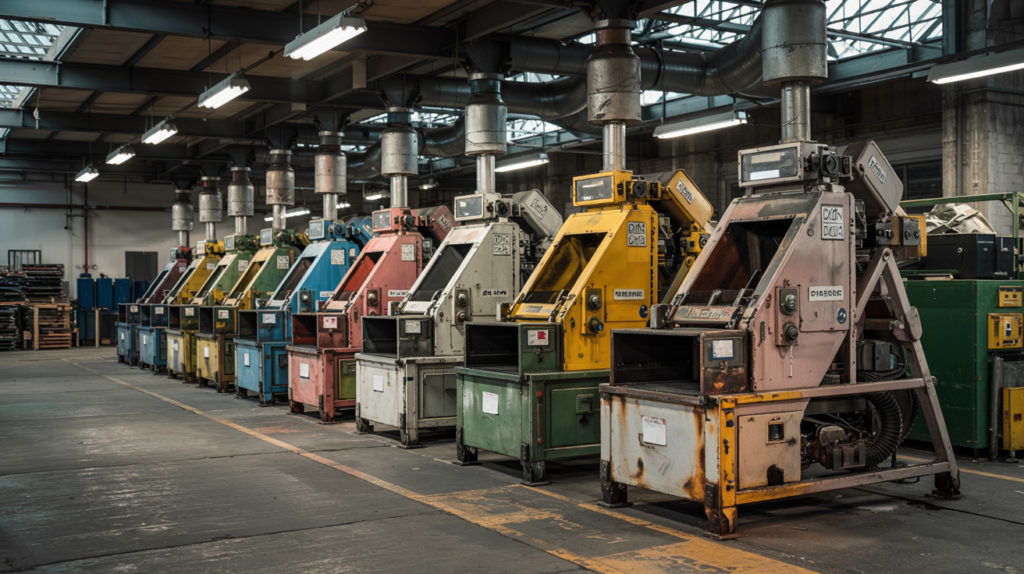
Mass production of golf tees requires industrial finishing equipment that would make your local woodworker’s shop look like a child’s toy set.
Semi-finished tees tumble inside massive sanding drums with the chaotic energy of a scramble tournament after an open bar. This process smooths every surface, ensuring your fingers won’t catch splinters when nervously fidgeting before attempting to drive the green. Sophisticated machinery separates perfect tees from those with microscopic flaws. The standard tee emerges measuring precisely 2.5 inches with consistency. Each weighs approximately 0.02 grams—lighter than your chances of making that 30-footer for eagle. Massive storage totes contain these processed treasures in bulk quantities. A single container holds roughly 100,000 finished tees—enough to supply your local muni for about three days, considering how many vanish into the rough.
Wooden Golf Tee Manufacturing: Painting and Finishing

The final transformation from bland wooden sticks to colorful little soldiers involves a paint party that would make Sherwin-Williams jealous.
Production staff load massive totes of unfinished tees into specialized paint drums with the efficiency of caddies calculating yardage. Technicians release gallons of colored paint into this wooden maelstrom. The rotation cycle continues for a significant period, ensuring complete coverage. Once thoroughly coated, these colorful creations require ample drying time. A protective enamel layer then enhances visuals and durability, creating a finish glossier than equipment catalog photos. The completed tees move to packaging, ready to meet their destiny: supporting golf balls for approximately 1.3 seconds before being lost forever in grass, broken in frustration, or pocketed by the guy who never brings his own equipment. Such a glorious but brief existence—not unlike your confidence after making one good swing on the range right before heading to the first tee.